Powrót do naturalnych czynników chłodniczych w oznacza także renesans popularności amoniaku (czynnik R717). To rozwiązanie wydaje pod względem parametrów cieplnych i niedrogie, ale jednocześnie czynnik toksyczny i wybuchowy. Dlatego w instalacjach pracujących z amoniakiem – szczególnie przemysłowych – konieczne jest skuteczne i efektywne wykrywanie wycieków amoniaku.
Amoniak (NH3), czyli czynnik chłodniczy R717, stanowi naturalny czynnik chłodniczym GWP =0 i znakomitych właściwościach termodynamicznych. Jednocześnie jednak jest gazem toksycznym i wybuchowym:
- najwyższe dopuszczalne stężenie (NDS) wynosi 14 mg/m3 ≈ 20 ppm, a najwyższe dopuszczalne stężenie chwilowe (NDSCh) to 28 mg/m3 ≈ 40 ppm;
- dolna granica wybuchowości (DGW) wynosi 15% = 150 000 ppm, a górna (GGW) to 33,6% = 336 000 ppm.
Wykrywanie wycieków amoniaku – przepisy
Dlatego przepisy prawa wymagają zabezpieczenia obiektów, w których stosowany jest amoniak jako czynnik chłodniczy:
- we wszystkich zakładach Rozporządzenie w sprawie ogólnych przepisów bezpieczeństwa i higieny pracy wymaga zastosowania urządzeń zapewniających sygnalizację o zagrożeniach.
- w browarach i fabrykach napojów gazowanych Rozporządzenie w sprawie bezpieczeństwa i higieny pracy w zakładach przemysłu piwowarskiego i napojów gazowanych stanowi: W przypadku chłodzenia pomieszczeń amoniakiem, w szczególności przy użyciu amoniakalnego urządzenia chłodniczego, pomieszczenia te wyposaża się w system wentylacji awaryjnej i stacjonarne analizatory, sygnalizujące sygnałem świetlnym lub dźwiękowym o przekroczeniu wartości najwyższego dopuszczalnego stężenia amoniaku.
- bhp zakładów rolno-przemysłowych reguluje Rozporządzenie w sprawie bezpieczeństwa i higieny pracy przy obsłudze amoniakalnych instalacji chłodniczych w zakładach przetwórstwa rolno-spożywczego, które stanowi: Maszynownię i aparatownię wyposażoną w aparaturę umożliwiającą ciągłą kontrolę stężeń amoniaku w powietrzu i sygnalizującą przekroczenie wartości najwyższego dopuszczalnego stężenia oraz najwyższego dopuszczalnego stężenia chwilowego amoniaku w powietrzu, wchodzącą w skład amoniakalnej instalacji chłodniczej, dopuszcza się do eksploatacji bez stałej obsługi.
Przepisy te wymagają, by zastosowano systemu detekcji amoniaku oraz nakazują monitorowanie i sygnalizowanie przekroczenia stężenia NDS i NDSCh. Oznacza to, że detektory amoniaku muszą wykonywać pomiar uśredniony i go sygnalizować (podane stężenia są bowiem wartościami średnimi, a nie bieżącymi).
Wymagania wobec systemów detekcji wycieków R717
Więcej o tym, jakie cechy powinien mieć system detekcji amoniaku mówią normy z grupy PN-EN 378-1+A1:2021 Instalacje chłodnicze
i pompy ciepła. Wymagania dotyczące bezpieczeństwa i ochrony środowiska. Przewidują one m.in.:
- powiadamianie lokalne i osób nadzoru,
- niezależne zasilanie systemu detekcji w stosunku do systemu maszynowni (możliwe do zrealizowania za pomocą zasilania rezerwowego),
- sygnalizację o 15 dB głośniejszą niż otaczające tło,
- sygnalizatory wewnątrz i na zewnątrz maszynowni,
- dla pomieszczeń kategorii „a” (ogólny dostęp) przekazywanie sygnału do pomieszczenia nadzoru,
- dla instalacji > 3000 kg przekazywanie alarmu do personelu, który powinien zareagować najpóźniej w ciągu 60 min,
- przy przekroczeniu limitu praktycznego dla maszynowni – sygnalizację alarmową oraz uruchomienie wentylacji,
- swobodny dostęp serwisowy,
- detekcję poziomu zagrożenia wybuchowego dla instalacji > 50 kg na poziomie do 30 000 ppm = 3%. Jest to wartość odpowiadająca 20% DGW. Przy tym poziomie następuje zatrzymanie pracy instalacji i wentylacji oraz odcięcie zasilania.
Ten ostatni parametr ma szczególne znaczenie, gdyż wprowadza dodatkowe zabezpieczenie pod kątem wybuchowym. Co więcej, jeśli w maszynowni znajdują się wyłącznie detektory stężeń toksycznych (NDS i NDSCh), przy nieco większym wycieku wskazania te zostaną przekroczone. Obsługa i służby ratownicze nie będą więc wiedzieć, jakie jest bieżące stężenie w pomieszczeniu i jakie działania powinny zostać podjęte. Natomiast drugi poziom detekcji (w zakresie 0–100% DGW) umożliwia bieżące monitorowanie sytuacji.
Bezpieczeństwo detekcji na pierwszym miejscu
Należy także zauważyć, że detektory powinny być urządzeniami w wykonaniu ATEX. Maszynownie bowiem najczęściej są objęte strefą zagrożenia wybuchem (np. przy suficie). A zgodnie z Rozporządzeniem MSWiA w sprawie ochrony przeciwpożarowej budynków, detektory stanowią wówczas urządzenia przeciwpożarowe. I jako takie powinny być wykonane zgodnie z projektem uzgodnionym przez rzeczoznawcę do spraw zabezpieczeń przeciwpożarowych. Co więcej, dopuszczenie do użytkowania możliwe jest tylko po odpowiednich próbach i badaniach potwierdzających prawidłowość ich działania. Ten zapis mówi o tym, jak ważne jest bezpieczeństwo w takich obiektach (zapewnia jest udział w procesie projektowym osoby z odpowiednimi uprawnieniami). Kwestią bezpieczeństwa należy kierować się także, projektując systemy detekcji w oparciu o certyfikaty produktów określające poziom bezpieczeństwa integralnego SIL (Safety Integrity Level). Dla systemów detekcji gazów optymalnym poziomem jest SIL2.
Do wykrywania amoniaku stosuje się najczęściej dwie uzupełniające się technologie sensorów elektrochemiczną (zakresy toksyczne) i katalityczną (zakresy wybuchowe).
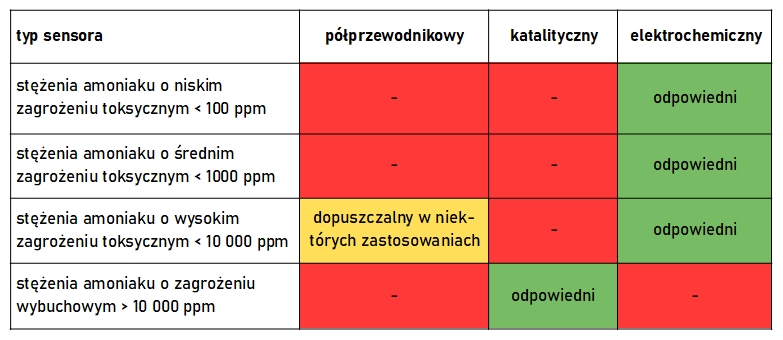
Gdzie instalować systemy wykrywania wycieków amoniaku
Dużym wyzwaniem jest prawidłowe rozmieszczenie detektorów. Norma PN-EN 378-3+A1:2021 podpowiada tylko, by rozmieścić je w miejscach potencjalnego gromadzenia się gazu. Nie jest to wcale oczywiste, tym bardziej, że wiele czynników (np. możliwe oblodzenie wlotów lub membrany detektora w mroźni) może zakłócić lub uniemożliwić pomiar.
Amoniak jest gazem lżejszym od powietrza, więc będzie się gromadził w najwyższych punkach. Zatem detektor wykrywający wyciek, chroniący produkty lub zabezpieczający przed wybuchem należy lokalizować przy suficie. Z kolei detektory odpowiedzialne za bezpieczeństwo osób trzeba zamontować na wysokości ok.150-180 cm od podłoża.
Należy unikać umieszczania gazów przy przepływie powietrza, w miejscach narażonych na oszronienie i/lub kondensację, np. za chłodnicami czy przy bramach. Przed problemem kondensacji w wilgotnych halach produkcyjnych częściowo chronią nasadki ochronne IP66. Nie rozwiązują one jednak problemu znacznej kondensacji lub oszronienia.
Projektując układ detektorów, trzeba też uwzględnić warunki eksploatacji. Oczywiste z pozoru umieszczenie detektora na suficie wysokiej chłodni może się okazać znacznym utrudnieniem dla serwisu. W chłodniach i mroźniach często stosuje się detektor z sensorem wyniesionym, wpuszczanym przez sufit. Wówczas można przeprowadzić serwisu z poddasza technologicznego.
Nie w każdym pomieszczeniu konieczny jest też detektor odpowiedni dla pomieszczeń ogólnodostępnych (kategoria „a”) czy z dostępem dozorowanym (kategoria „b”). W pomieszczeniach z dostępem kontrolowanym (kategoria „c”) nie są potrzebne urządzenia tak samo czułe i o tak samo niskim progu jak w pomieszczeniach produkcyjnych z dostępem dozorowanym. Można także uzupełnić progi alarmowe wymagane do sygnalizowania poziomów ostrzegawczych o dodatkowe progi, uruchamiające urządzenia wykonawcze (wentylacja mechaniczna, sygnalizacja czy odłączanie prac układu). Czterostopniowa ochrona pozwala zoptymalizować progi alarmowe. Wówczas przy zachowaniu pełnego bezpieczeństwa ludzi nie następuje paraliż pracy zakładu w przypadku incydentu czy fałszywego alarmu.
Metryczka artykułu
Opracowanie: Michał Domin, PT Signal. Pełna (pierwotna) wersja materiału ukazała się w numerze 6/2023 magazynu Rynek Instalacyjny. Zalogowani użytkownicy mogą także przeczytać tekst na portalu „Rynek Instalacyjny”.
Zdjęcie główne: Gazex (kontroler wentylacji WG.EX oraz detektor progowy DEX/F)